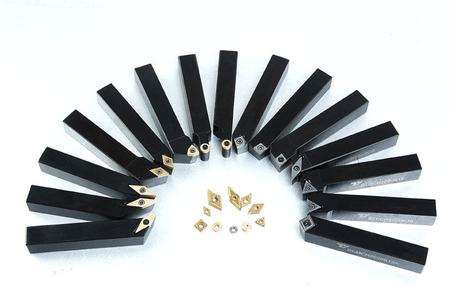
First, the tool compensation proposed:
Using an end mill to machine a workpiece on a CNC machine tool, it can be clearly seen that the tool center movement gauge does not coincide with the contour of the workpiece. This is because the workpiece contour is formed by the movement envelope of the end mill. The center of the end mill is called the cutter location (4, 5 coordinate CNC machine tool is called cutter location vector), and the movement track of the cutter location represents the tool's trajectory. In NC
Machining, programs are programmed according to the contour size of the workpiece or programmed according to the trajectory dimension of the tool location. This should be handled according to the specific situation.
CNC machine tool end mill processing
In the full-function CNC machine tool, the CNC system has tool compensation function, which can be programmed according to the workpiece contour size. After the tool compensation is established and executed, the CNC system automatically calculates and the tool position is automatically adjusted to the tool movement path. By directly using the workpiece size to compile the machining program, the tool wears, and the replacement machining program does not change. Therefore, the use is simple and convenient.
Economical CNC machine tools are simple in structure, low in price, and have a certain amount of ownership in production enterprises. In the economical CNC machine tool system, if there is no tool compensation function, the machining program can only be programmed according to the trajectory size of the tool location. This requires that the trajectory size of the tool location should be calculated based on the workpiece contour size and tool diameter. Therefore, the calculation volume is large and complex, and the tool wear and replacement need to recalculate the trajectory size of the tool location and reprogram the machining program.
Second, the tool compensation in the full-function CNC machine tool system:
1. CNC lathe tool compensation
The CNC lathe tool compensation includes tool position compensation and tool arc radius compensation. In the machining program, it is specified by T function. The first two XX in T***X are the tool number, and the last two XX are the tool compensation number, such as T0202. If the tool offset number is 00, tool offset is canceled.
(1) Tool position compensation Tool wear or tool position change caused by reinstallation of the tool. After the tool position compensation is established and executed, the machining program does not need to be reprogrammed. The method is to measure the position of each tool and input it into the specified memory. After the program executes the tool compensation command, the actual position of the tool replaces the original position.
If there is no tool compensation, the tool moves from 0 to 1 point. The corresponding block is N60G00C45X93T0200. If the tool compensation is X=3 and Z=4, it will be stored in the corresponding compensation memory. After the tool compensation is executed, the tool will be from 0 point. Move to 2 instead of 1 and the corresponding block is N60G00X45Z93T0202.
(2) Tool arc radius compensation When programming a CNC lathe, the tool nose is regarded as a point (imaginary point P), but in fact, in order to improve the tool life and reduce the surface roughness of the workpiece, the vehicle The tip of the knife is ground to a radius with a small radius (blade tip AB arc), which inevitably results in a shape error of the machined workpiece. On the other hand, the position of the tool nose arc, the shape of the turning tool will also have an impact on the workpiece processing, and these can be solved by tool arc radius compensation. The shape and position parameters of the turning tool are called the tool nose orientation and are represented by parameters 0 to 9. P point is the theoretical tool tip point.
(3) Tool offset parameters Each tool offset number corresponds to 4 parameters of tool position compensation (X and Z values) and tool arc radius compensation (R and T values), and is input to the corresponding memory before machining and displayed on the CRT. . In the automatic execution process, the numerical control system automatically corrects the position error of the tool and automatically performs the tool nose arc radius compensation according to the values of X, Z, R, and T in the memory.
2. Machining Center,
CNC Milling Tool Compensation
CNC system of machining center and CNC milling machine, tool compensation function including tool radius compensation, included angle compensation and length compensation tool compensation function.
(1) Tool radius compensation (G41, G42, G40) The tool radius value is stored in the memory HXX in advance, and XX is the memory number. After executing tool radius compensation, the CNC system automatically calculates and automatically compensates the tool according to the calculation result. The tool radius left compensation (G41) refers to the tool deviation to the left of the programmed machining path movement direction, and the tool radius right compensation (G42) refers to the tool deviation to the right of the programmed machining path movement direction. G40 can be canceled for tool radius compensation, and H00 can be used to cancel tool radius compensation.
It should be noted during use: when creating or canceling tool compensation, the G01 or G42 command must be used for the G41 or G42 command block. G02 or G03 must not be used. When the tool radius compensation takes a negative value, the functions of G41 and G42 are used. exchange.
Tool radius compensation has two compensation modes: B function and C function. Since the B function tool radius compensation only performs tool compensation calculation according to the program of this paragraph, it can not solve the transition problem between the program segments. It is required to process the contour of the workpiece into a round transition. Therefore, the craft corner of the workpiece is not good, C function tool radius The compensation can automatically handle the transfer of the tool center trajectory of the two blocks, and can be programmed completely according to the contour of the workpiece. Therefore, almost all modern CNC machine tools use C function tool radius compensation. At this time, the following two program segments that require the establishment of a tool radius compensation program must have displacement instructions (G00, G01, G02, G03, etc.) that specify the compensation plane. Otherwise, the correct tool compensation cannot be established.
(2) Inclusion angle compensation (G39) The intersection between the two planes is the included angle. Over-cutting may occur, resulting in machining error. The angle compensation (G39) can be used to solve this problem. When using the angle compensation (G39) instruction, it should be noted that this instruction is not modal and is only valid within the instruction block. It can only be used after the G41 and G42 instructions.
(3) Tool length offset (G43, G44, G49) The tool length offset (G43, G44) command can compensate the change in the tool length at any time without changing the program, and the compensation amount is stored in the memory of the H code command. G43 indicates that the amount of compensation in the memory is added to the coordinate value of the end point of the program instruction. G44 indicates the subtraction. To cancel the tool length offset, G49 or H00 can be used. In block N80G43Z56H05 and in, if the value in the 05 memory is 16, then the end point coordinate value is 72mm.
The value of the amount of compensation in the memory can be pre-stored in the memory with MDI or DPL. The block instruction G10P05R16.0 can also be used to indicate that the compensation amount in memory No. 05 is 16 mm.
Three, economical CNC machine tool trajectory calculation:
The economical CNC machine tool system, if there is no tool compensation command, can only calculate the trajectory size of the tool location, and then press this to program or perform local compensation processing.
1. Tool Center (Knife Site) Trajectory Calculation
In a numerical control system that needs to calculate the tool center trajectory, the coordinates of the base point and the node on the tool center corresponding to the base point and the node of the part contour are calculated. Tool center motion path for machining workpiece curve with φ8 end mill. It can be seen that the tool movement path is the contour line of the part contour, which can be obtained from the part contour and the tool radius.
Straight line equation of the equidistance line:
When the desired equidistance line is above the original line, it takes the "+" sign and vice versa.
Round isometric line equations:
When the equidistance line is equal to the outer equidistance line, it takes the "+" sign and vice versa.
To solve the coordinates of the base point on the equidistant line, simply solve the equation for the relevant equidistance line. For example, find the coordinates of the 3' point, the 2 point coordinate (40, 85), and the 3 point coordinate (70, 105).
A=y2-y3=-20
B=x3-x2=30
C=x3y2-ybx2=1750
Find the center coordinates (85,105).
Two equidistance line equations:
-20x 30y=1750 144.222
(x-85)(y-105)=(15 4)
Solve for x=66.134y=107.231
That is, the coordinate of the 3′ point is (66.34, 107.231). The coordinates of other base points or nodes on the tool center trajectory can be obtained by the same method, and then press this to program.
2. Calculating the Offset of the Tool Knife Point in CNC Lathe
In the numerical control turning process, in order to facilitate the tool, the tool is often set with the imaginary tool tip P point. If there is no tip radius compensation, undercut will occur when turning cones or arcs. When the part requires high accuracy and has a cone or arc, the solution is: calculate the center of the arc radius of the tool nose, and then click this to calculate the local compensation.
To compensate for the tool position caused by the radius r of the tool tip when turning the surface. When tool position compensation is performed in the Z direction and X direction at the same time, the actual contact point of the blade with the workpiece moves to the tool tip set point P during programming, and the compensation amount of r can be calculated as follows:
When compiling the machining workpiece cone surface program, the base point coordinates are the compensation coordinates (Z and X) of the workpiece contour base point coordinates (Z and X) plus the radius of the cutting edge arc radius r (Dz and DX), thus solving the problem of no tip radius compensation The problem.
In NC machining, because the tool tip has a circular arc, the contour of the workpiece is formed by the tool motion envelope. Therefore, the motion path of the tool point is not coincident with the contour of the workpiece. In the full-function CNC system, its tool compensation command can be applied. According to the workpiece contour size, it is convenient to program and process. In the economical numerical control system, the trajectory of the tool location can be calculated based on the workpiece contour size, tool, etc., and programming can be done according to the method of local compensation.